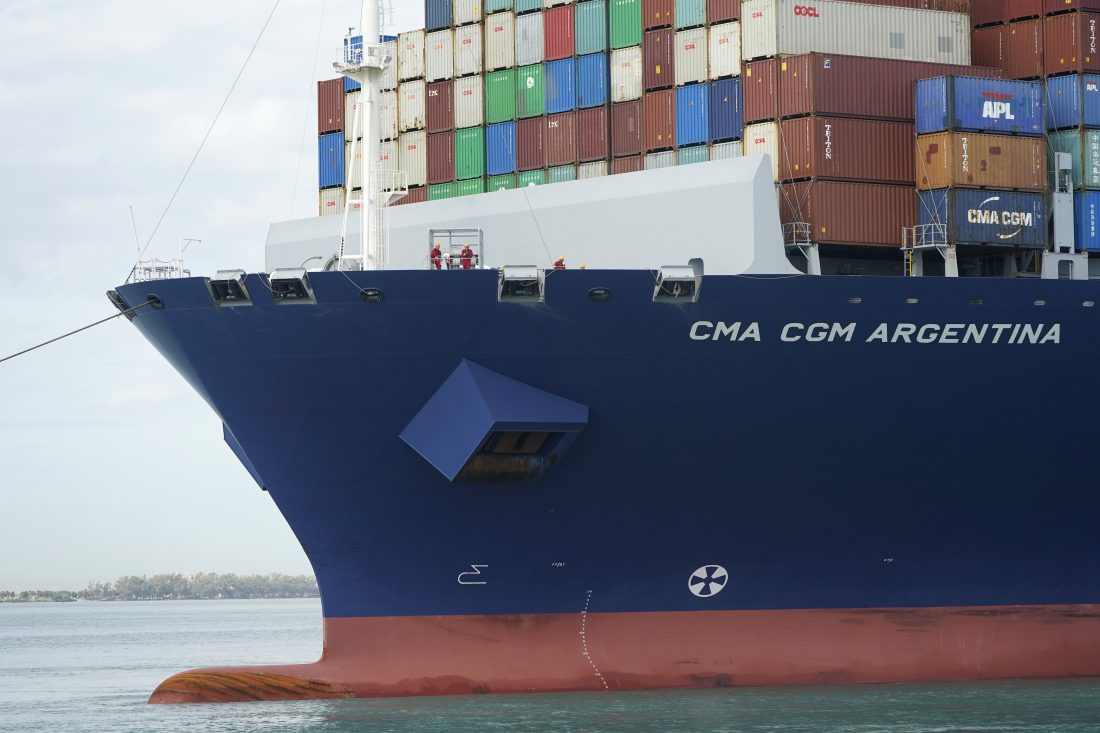

In this April 6, 2021 photograph, crew users stand on the bow as the CMA CGM Argentina arrives at PortMiami, the most significant container ship to call at a Florida port in Miami. Importers are contending with a excellent storm of provide trouble — increasing rates, overcome ports, a shortage of ships, trains, vans — that is anticipated to past into 2022. (AP Image/Lynne Sladky)

WASHINGTON — Match maker Eric Poses previous calendar year established The Worst-Circumstance Situation Card Activity, building a wry reference to the way the coronavirus experienced upended standard existence.
He experienced no plan.
In a twist that Poses hardly ever could have predicted, his sport itself would come to be caught up in the latest fallout from the overall health crisis: a backlogged world wide offer chain that has delayed shipments around the globe and despatched freight fees rocketing.
Worst-Circumstance Situation, made in China, was supposed to achieve U.S. retailer Target’s distribution facilities in early June. Alternatively, the video games ended up trapped for weeks at the Port of Seattle and did not get there right until mid-July.
“It’s consuming my life,” said Poses, who commenced his Miami Seaside, Florida-based mostly toy enterprise All Things Equivalent in 1997, promoting video games from the trunk of his automobile. “You do every little thing appropriate. You produce on time. You’re psyched about your products.”
And then … unforeseeable disaster.
Like other importers, Poses is contending with a great storm of source trouble — climbing rates, confused ports, a lack of ships, trains, vans — that is predicted to final into 2022. The expertise proved disturbing adequate that Poses is reconsidering a cost-saving choice he designed 5 yrs ago: to shift output of his games and toys out of the United States to China. Now, he thinks, it could possibly make sense to deliver manufacturing again — at the very least to Mexico, if not the United States — to shield him from the challenges of relying on factories an ocean away in China.
“I’m keen to make smaller sized margins,” he said, “if it indicates considerably less anxiousness.”
Other American corporations are making related calculations: 52% of the U.S. production executives surveyed by the consulting agency Kearney stated they have commenced obtaining a lot more materials in the United States in response to COVID-connected supply disruptions. Forty-seven p.c claimed they system to lower reliance on supplies or factories from a one state 41% precisely mentioned they needed to slash their dependence on China.
And not just since of the virus-linked bottlenecks in shipping, severe as they are. Organizations are worried, far too, about getting caught in the crossfire of a trade war between the United States and China, the world’s two most important economies.
The conflict began when President Donald Trump imposed taxes on $360 billion value of Chinese imports to protest Beijing’s combative work to surpass American technological dominance.
But neither Chinese leader Xi Jinping nor Trump’s successor, Joe Biden, seems to be in a hurry to find peace.
“The complete connection is in undesirable form,” reported Rosemary Coates, a longtime guide to corporations wanting to set up factories in China.
In The united states, there is bipartisan disappointment around China’s sharp-elbowed trade practices — which, critics say, incorporates cybertheft — as nicely as its crackdown on civil liberties in Hong Kong, repression of Muslims in Xinjiang and bullying of neighbors in South and Southeast Asia.
“Are we in a 21st century model of the Chilly War? Of course,” claimed trade attorney Michael Taylor, a lover at King & Spalding. “The endgame is not nuclear annihilation. The endgame now is financial dominance.”
For decades, companies have piled up revenue by going manufacturing to China and other small-wage nations around the world, then exporting their merchandise back again to the United States. They have also held down costs by trying to keep inventories to a bare minimum. Below a “just-in-time” approach, factories get components only as they will need them to meet up with orders.
But relying on distant factories and preserving inventories threadbare is risky. In March 2011, an earthquake and tsunami ruined auto sections plants in northwestern Japan. The resulting components shortages temporarily idled auto vegetation close to the world, which includes some in the United States — a sobering reminder that prolonged supply chains are susceptible to disruption.
Then arrived Trump’s trade war. Importers scrambled to reconfigure their source chains and find alternatives to Chinese factories just after Trump imposed rigid tariffs on items from China.
But they’d in no way seen anything like what COVID-19 inflicted on world commerce.
As nations locked down and households took refuge at property in February and March past yr, providers sold off inventories and canceled orders from suppliers. And the economy did, in fact, collapse: In the United States, gross domestic merchandise, the broadest measure of economic output, fell at a 31.2% annual level from April by way of June 2020 — the worst quarter in records dating to 1947.
Then something unexpected occurred.
“What no one understood was that when you deliver all people household, the very first factor we all do is shop” on-line, explained Lewis Black, CEO of Almonty Industries, which mines the uncommon metallic tungsten. “You had, on a person hand, inventories staying operate down and producing floor to a halt, and on the other, persons ended up paying out like insane.”
Fueled by pent-up client need, specially as vaccines authorized economies to reopen and households to get again outside once more, progress roared back. The U.S. overall economy expanded at a stunning clip — a record yearly fee of 33.8% from July via September 2020 — and saved chugging alongside, most lately registering a balanced 6.5% yearly development fee from April as a result of June this year.
Suddenly, companies have been confused with orders they could not satisfy.
“They experienced an oops moment,” Black mentioned.
“It’s a typical scenario of overreacting on the front finish and getting to perform catchup,” mentioned Tom Derry, CEO of the Institute for Supply Management, an affiliation of paying for professionals. “No one definitely foresaw the strength in the surge of demand from customers …. Supply just just can’t preserve up.”
As companies hurried to fulfill surging desire, the charge of uncooked resources soared: The price tag of oil is up a lot more than 70% more than the previous 12 months, aluminum 55%. Tin prices have doubled. The value of large density polyethylene blow-molded plastic — common in bottles, fuel tanks, industrial drums and other products — has surged 157%, in accordance to the Plastics Exchange place industry.
Freight expenditures shot up, also, as corporations tried using to e book transport containers. The Baltic Dry Index, which measures delivery charges, has rocketed additional than 700% considering the fact that mid-May perhaps 2020.
Acquiring products on to container ships was hard. But that wasn’t the conclusion of the trouble. Ports ended up overwhelmed when the cargo arrived.
“They couldn’t get the ships in and out,” stated Richard Gottlieb, CEO of the consultancy Global Toy Specialists. “They ended up backed up. You know that terrible experience where your plane lands and there’s no open up gate? Which is what took place to containers.”
The final result is that the provide chain breakdown is paralyzing a lot of corporations.
Look at Elmer Schultz Services, a Philadelphia company that repairs and maintains kitchen machines for restaurants and other consumers. It is going through maddening delays in finding components. It employed to get 7 to 10 days to get backordered pieces. Now, it normally takes 3 or four weeks.
“It’s incredibly annoying to explain to a client we simply cannot take care of their oven for three or 4 weeks,” claimed Kirby Mallon, president of Elmer Schultz and of the trade team Industrial Food stuff Machines Assistance Affiliation.
Glitches made matters worse. The enormous container ship Ever Specified obtained stuck in the Suez canal for a week in March, chopping off shipping and delivery between Asia and Europe. The world’s fourth-busiest port — Yantian near the Chinese producing middle Shenzhen — was shut down for a month by a resurgence of COVID cases in late May perhaps.
“When you give up your very own manufacturing and allow any person manufacture for you — if it all goes well, you can make far more revenue. But the motive you can make more funds is there is more possibility,” claimed Taylor, the trade attorney. “And that chance is source disruptions, labor challenges, good quality management, theft of your” intellectual assets.
Importers tried using to determine how considerably of the better prices they could go on to their consumers. At Mindscope Products near Los Angeles, owner George Balanchi wants to stay clear of elevating the price ranges he fees stores for his company’s toys, together with distant-controlled automobiles and the Jabberin’ Jack talking pumpkin.
“It’s tricky,” he stated.
Boosting price ranges, he stated, is less difficult on line. He has upped the on line value of Mindscope’s radio-handle stunt car to $22.99 from $19.99 and ideas one more price hike to $24.99 next 12 months.
Firms that resisted shifting creation abroad now take pleasure in an edge. They really don’t have to wait around for their products and solutions to cross the ocean — or figure out irrespective of whether they can go along to prospects the import taxes that strike them at the U.S. border.
“The fellas who stuck through the hard time when their opponents experienced enormous financial gain margins now glimpse like they have been smarter than every person considered they were,” Taylor said.
Make-A-Fort in Wichita, Kansas, is one of the fortunate — or visionary — kinds. Co-founder Kent Johnson determined to make his company’s solutions — easy-to-assemble cardboard fortresses to participate in in — in the United States. He did not like the extended lead times essential for production overseas. He wished much more regulate about the top quality of the merchandise and wanted to be ready go to the assembly lines consistently.
And he needed to maintain careers in America.
“We began out executing it at a drawback,” he explained. “We just got a little little bit lucky. We don’t have a ton of offer chains.”
Freight charges are way up in the United States, he explained, but which is still nothing at all like the exploding expense of shipping containers.
Mursix Corp., which makes precision metal elements for the automobile and healthcare industries, has been pounded by better metal expenditures and shipping bottlenecks.
“We utilised to be ready to set anything on a boat and get it in five to seven months,” said Andy Dieringer, director of offer chain for the Yorktown, Indiana, firm. Now, it can take 9 to 11 months for shipments to arrive from China.
As a final result, the organization is hunting for new suppliers in Mexico, mentioned company co-owner Susan Murray Carlock, also vice president of company progress. “I could see us being in a position to get there by next year” — possibly by the 2nd quarter of 2022, she claimed.
But leaving China is not straightforward. Costs there remain small. And specialized suppliers cluster in Chinese producing centers, producing it straightforward for factories to get components when they want them.
At All Things Equivalent, for case in point, Poses laments that “I have not still had luck in obtaining a North American factory to produce my online games at a aggressive cost. But, I’m still hoping!”
“There are zillions of components that are not manufactured in the U.S. and possibly will not be produced in the U.S. since they’re reduced-charge elements and because the marketplace is so vertically built-in,” said Coates, the specialist, who is executive director of the Reshoring Institute, a nonprofit that will help corporations manufacture in the United States.
It can also be dangerous. Corporations may possibly be compelled to leave devices at the rear of, raising the chance that the Chinese workers they’ve qualified can set the deserted molds and device applications to operate cranking out competing products and solutions.
“It’s sophisticated to extract your self from China,” Coates reported, “and typically extremely highly-priced.”
But rising recognition of the threats of based on provides that need to cross a broad ocean — especially at a time of U.S.-China tensions — is building U.S. companies glimpse for alternate options nearer to residence. Just after all, significant source chain disruptions are turning into much more common, the consulting company McKinsey has observed
”Although COVID feels like such a black swan — and it is — disruptions in offer chains have been raising in severity and frequency,” explained Katy George, a McKinsey spouse.
The moment rare, source chain breakdowns that previous a month or more are now happening each 3.7 years, McKinsey identified, noting in a report that “a single extreme celebration that disrupts output for 100 times — something that transpires every 5 to 7 years on normal — could erase almost a year’s earnings in some industries.”